Predictive motor maintenance is a proactive strategy that analyzes data to forecast when equipment may break.
Need Motor Control Products?
Get Your QuoteSell To Us
Got Electrical Equipment You Don't Need?

Reduce Your Electrical Inventories & Earn Cash
Sell My EquipmentPanelboard
Need a Panelboard for Your Project/Job?

Our Experienced Sales Engineers Can Help Design the Right Panelboard For You
Learn MoreTransformer Oil Testing
Is Your Transformer Due For Servicing?

Get Your Oil Analysis & Fluid Testing Done By Our NETA-Certified Techs
Learn MoreElectrical Product Resources
Product Training Product Safety Product Guides Product News Featured ProductsUnderstanding Predictive Electric Motor Maintenance
Predictive maintenance is a proactive strategy that analyzes data to forecast when equipment may break. Unlike reactive maintenance, which handles issues after they arise, or preventive maintenance, which is conducted on a regular basis, predictive maintenance enables you to address possible problems before they become serious.
Electric motor predictive maintenance saves you money on maintenance, extends the life of your equipment, and reduces downtime. This strategy is extremely useful in industrial automation, where ongoing operation is important. Predictive maintenance for electric motors allows you to keep ahead of problems for smooth and continuous operations.
Implementation of Predictive Maintenance Strategies
There are plenty critical steps when using a predictive maintenance approach in motor control centers. First, evaluate your present maintenance processes and determine which equipment might benefit the most from predictive maintenance. Next, collect information about the operating performance of your equipment.
Create a strategy that includes the necessary equipment, advances in technology, and staff to do predictive maintenance. Successful implementation frequently involves case studies of other companies that have successfully implemented predictive maintenance, that may provide you with useful information and best practices. By following this electric motor predictive and preventive maintenance guidance, you may develop a tailored approach that meets your individual requirements.
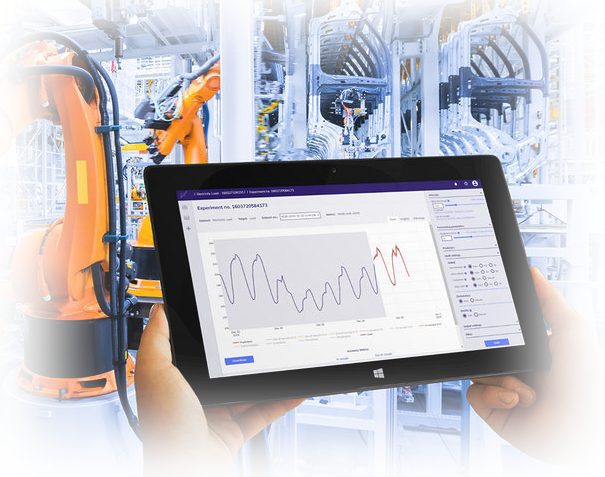
Using Sensor Data and Advanced Diagnostics
Sensor data is the basis of predictive electric motor maintenance. Various types of sensors, like vibration and temperature sensors, are critical in monitoring motor health. These sensors capture information about the state of your motors that can be used to predict likely breakdowns.
Advanced diagnostics, including electrical motor current measurement for predictive maintenance, machine learning, and artificial intelligence (AI), can help you evaluate this data. These technologies help with identifying trends and anomalies that may show oncoming concerns, allowing you to take action before a breakdown happens. This predictive maintenance for electric motors guarantees that your equipment remains in top shape. This predictive maintenance for electric motors helps your equipment remain in top condition.
Proactive Electric Motor Health Management
Managing motor health proactively plays an important part in industrial automation. By monitoring motor health in real-time, you can spot possible issues before they occur. This lets users schedule maintenance tasks during planned downtime, reducing disruption to your operations.
Adding predictive maintenance for electrical motors into your current industrial automation systems makes sure smooth operation and maximum efficiency. This proactive approach not just increases dependability but also improves the overall performance of your system, making predictive maintenance for electrical motors an essential component of your maintenance plan.
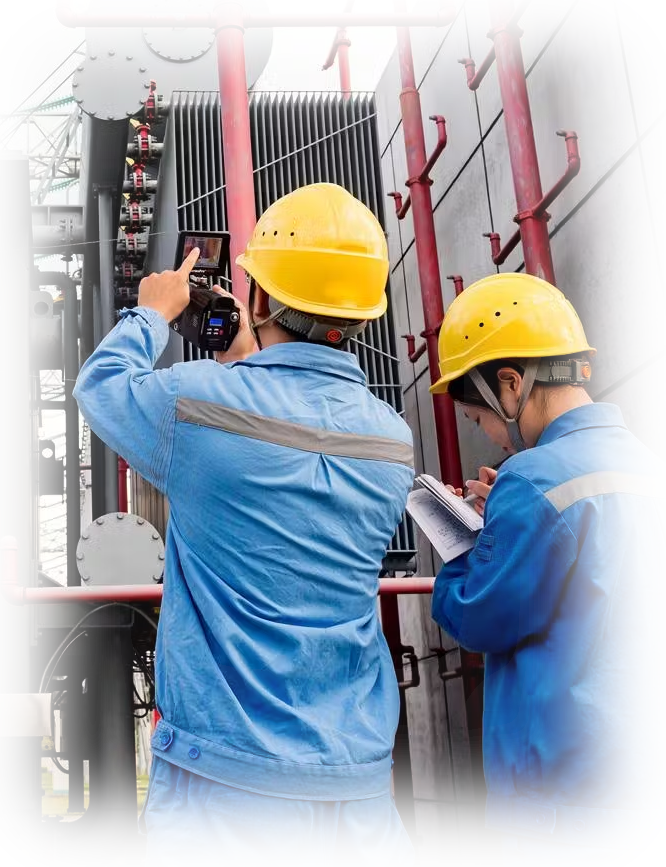
Future Trends in Predictive Electric Motor Maintenance
The future of predictive maintenance seems hopeful as new technologies advance within the industry. Sensor technologies, data analytics, and machine learning advancements can help you forecast and avoid equipment problems.
Keeping up with advances in motor diagnostics and industrial automation can help you stay competitive. As these technologies advance, they will provide increasingly more accurate and effective methods of maintaining your equipment and sustaining reliability. Include the latest trends in electrical motors’ predictive maintenance to keep your operations ahead of the curve.
ELECTRICAL PART | PREDICTIVE MAINTENANCE BENEFITS |
Motor Starters | Predictive maintenance identifies wear and tear on motor starters before they fail, providing continuous functioning and increasing their lifespan. Regular monitoring eliminates unexpected downtime and lowers repair costs. |
Variable Frequency Drives | By monitoring the performance of VFDs, predictive maintenance may spot imperfections and inefficiencies early, improving their operation and energy use and avoiding costly failures. |
Combination Starters | Predictive maintenance offers early diagnosis of difficulties with combo starters, such as overheating or electrical failures, maintaining dependable motor control, and lowering the risk of operating disruptions. |
Motor Contactors | Regular monitoring of motor contactors helps in detecting contact wear and potential problems, preventing malfunctions, and assuring consistent and dependable motor performance. |
VFDs | Predictive maintenance, like variable frequency drives, allows proactive adjustments and repairs, boosting efficiency, lowering energy usage, and preventing unexpected breakdowns. |
PLCs (Programmable Logic Controllers) | Predictive maintenance of PLCs involves tracking their performance and condition so they run without faults, consequently preserving the entire system’s dependability and performance. |
Control Relays | By forecasting control relay failure, maintenance may be conducted before the failure occurs, reducing downtime and making sure you have smooth control functioning. |
Motor Control Centers | Predictive maintenance helps in the detection of difficulties in motor control centers that include loose connections or component degradation, resulting in optimal performance and avoiding large-scale operational interruptions. |
Don’t Wait for Electrical Equipment Failures to Occur
Predictive maintenance based on motor diagnostics is an effective technique for providing reliability in industrial automation. Understanding and executing predictive maintenance, using sensor data and sophisticated diagnostics, and proactively controlling motor health will help you decrease downtime and lengthen the life of your machines.
Don’t wait for failures to occur – start predicting and preventing them today.