PLCs (Programmable Logic Controls) function as a central hub, overseeing motor control and motor automation.
Need PLC Products For Your Project?
Get A QuoteSell To Us
Got Electrical Equipment You Don't Need?

Reduce Your Electrical Inventories & Earn Cash
Sell My EquipmentPanelboard
Need a Panelboard for Your Project/Job?

Our Experienced Sales Engineers Can Help Design the Right Panelboard For You
Learn MoreTransformer Oil Testing
Is Your Transformer Due For Servicing?

Get Your Oil Analysis & Fluid Testing Done By Our NETA-Certified Techs
Learn MoreElectrical Product Resources
Product Training Product Safety Product Guides Product News Featured ProductsPLCs for motor control process inputs from sensors throughout industrial equipment. These inputs detect factors like temperature, pressure, and motion to inform the PLC for industrial motor control. Manufacturing with PLC-Based motor control means that configured logic sends outputs directing the motor’s actions, implementing motor control programming. These commands, like industrial motor control, decide when to start or stop the motor, adjust its speed, or change its direction. Simply put… PLCs simplify motor control for industrial automation.
PLCs for Motor Control: Real-World Applications
Elevator Control System: Next time you take an elevator in a high-rise building, thank PLCs for a smooth ride. These elevators use a control system similar to a PLC to regulate elevator car movement, door operation, and floor selection.
Industrial Motor Applications: Consider an industrial scenario with a conveyor belt system in a manufacturing factory. PLC programming is utilized to regulate the conveyor belts’ speed and direction, resulting in smooth material handling and efficient production processes. PLC programming regulates the horizontal movement of items along conveyor belts in the same way elevator control systems control the vertical movement of humans.
Home HVAC System: Consider your home’s thermostat, which controls the heating, ventilation, and air conditioning (HVAC) system. The thermostat employs programming logic to maintain the needed temperature by changing the HVAC equipment. And how about a large-scale HVAC system in a commercial or manufacturing facility? PLC programming controls the functioning of industrial fans, pumps, and compressors to regulate the facility’s temperature and air quality. PLC programming guarantees optimal conditions in industrial locations, much like a thermostat does in your home.
Food and Beverage Production: A large-scale coffee production line may exist within a food processing factory. PLC programming controls the operations of industrial coffee grinders, mixers, and packaging equipment. Just as your automatic coffee maker offers consistency and efficiency when preparing your morning cup, PLC programming makes precise control and automation possible in industrial coffee manufacturing.
PLC 5-Step Process
Input Gathering: PLC collects data from sensors and switches, like detecting temperature or motion.
Processing: PLC receives inputs using programmed logic, making decisions based on predefined conditions and instructions.
Logic Execution: Based on the processed inputs, PLC executes specific actions or commands, like starting or stopping a motor.
Output Generation: PLC sends signals to control devices like motors, valves, or lights, translating decisions into physical actions within the system.
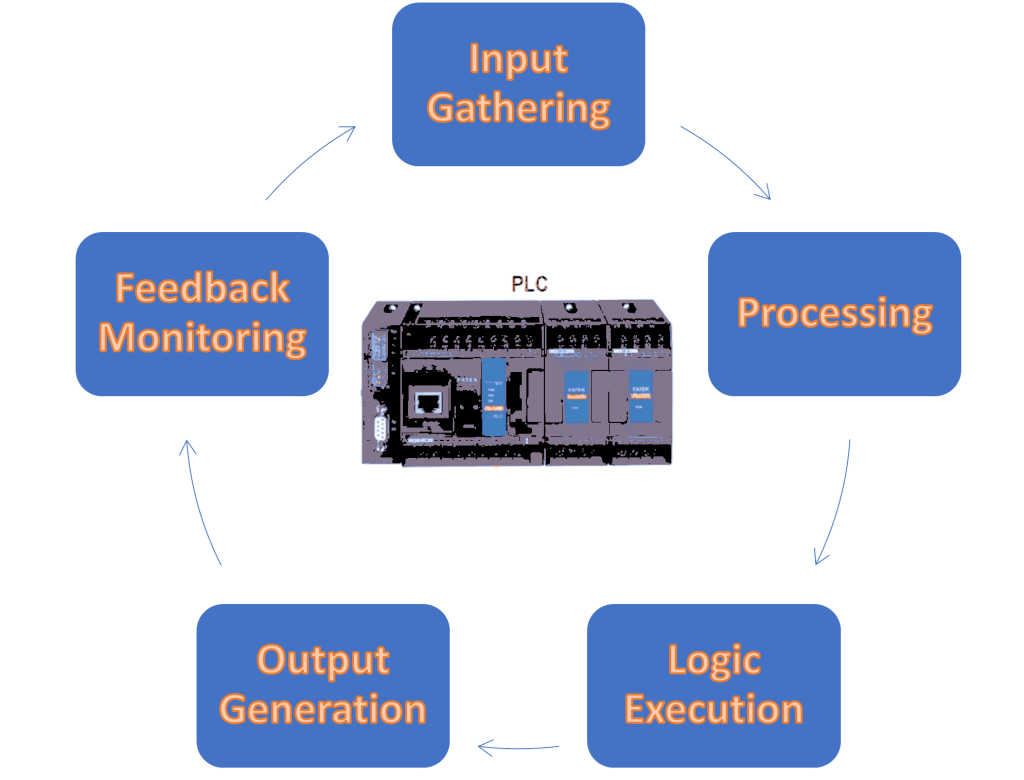
Feedback Monitoring: PLC continuously monitors the system’s feedback, outputs match desired conditions, and adjusts operations for best performance.
4 Popular PLC OEM Product Series to Control Production
Allen-Bradley ControlLogix PLC Series
If you’re looking for a PLC products for motor control, Allen Bradley ControlLogix PLC is a scalable and modular platform that adapts to applications. It has I/O capabilities, so you have the flexibility to connect numerous devices seamlessly. Advanced communication options allow smooth integration into your existing network infrastructure. ControlLogix PLCs are reliable for uninterrupted operations. They’re compatible with various programming software for easier implementation.
PART/MODEL NUMBERS:
ControlLogix 1756-L71
ControlLogix 1756-L72
ControlLogix 1756-L73
ControlLogix 1756-L74
ControlLogix 1756-L75
Allen-Bradley CompactLogix PLC Series
When space is limited without compromising performance, Allen Bradley CompactLogix series is for standalone machines or OEM applications. The CompactLogix PLC series gives flexibility and performance in a smaller footprint.
PART/MODEL NUMBERS:
CompactLogix 1769-L24ER-QB1B
CompactLogix 1769-L27ERM-QBFC1B
CompactLogix 1769-L30ER
CompactLogix 1769-L32E
CompactLogix 1769-L33ER
Siemens SIMATIC S7-1500 Series PLC Series
This PLC solution can handle demanding industrial automation tasks. The SIMATIC S7-1500 high-performance controllers have lightning-fast processing for quick and precise control. SIMATIC S7-1500 Communication options integrate with your existing network infrastructure. Cybersecurity features protect data and systems against threats. The flexibility and scalability of the SIMATIC S7-1500 series mean that it grows with you in the most complex control systems.
PART/MODEL NUMBERS:
SIMATIC S7-1500 CPU 1511-1 PN
SIMATIC S7-1500 CPU 1513-1 PN
SIMATIC S7-1500 CPU 1515-2 PN
SIMATIC S7-1500 CPU 1516-3 PN/DP
SIMATIC S7-1500 CPU 1518-4 PN/DP
Siemens SIMATIC S7-1200 PLC Series
For small to medium-sized projects, SIMATIC S7-1200 series controllers offer integrated functionality. Onboard digital and analog I/O give versatility to handle basic to moderate automation tasks. Communication ports allow for seamless connectivity to other devices and systems. Easy programming capabilities for automating a single machine or a small production line.
PART/MODEL NUMBERS:
SIMATIC S7-1200 CPU 1211C
SIMATIC S7-1200 CPU 1212C
SIMATIC S7-1200 CPU 1214C
SIMATIC S7-1200 CPU 1215C
SIMATIC S7-1200 CPU 1217C
Case Studies in PLCs for Industrial Automation
Case | Problem | Solution |
Optimizing Energy Consumption in a Manufacturing Plant | High energy costs due to inefficient machinery and equipment utilization | Implementation of PLC programming to control and optimize equipment operation based on real-time energy consumption data, resulting in significant cost reduction. |
Enhancing Safety in a Chemical Processing Facility | Safety concerns related to manual handling of hazardous materials and equipment malfunctions | Utilization of PLC programming to automate critical safety processes, such as emergency shutdown systems and leak detection alarms, ensuring a safer working environment. |
Improving Production Efficiency in an Automotive Assembly Line | Bottlenecks and production delays caused by manual processes and inconsistent workflows | Deployment of PLC programming to streamline production processes, synchronize equipment operation, and optimize sequencing and timing of tasks, leading to increased efficiency. |
Upgrading Industrial Motor Controls and PLC Hardware
When replacing a legacy older electrical motor and PLC programming, consider the following factors to ensure a seamless transition and optimal performance:
Electric Motor and PLC Compatibility
Is the new motor compatible with the existing electrical infrastructure, like voltage and power supply requirements?
Will the replacement PLC be compatible with the communication protocols and I/O modules of the legacy system?
Motor Functionality and PLC Performance
Does the new motor meet the performance requirements and specifications of the application, such as speed, torque, and efficiency?
Will the replacement PLC have enough processing power and memory capacity to handle the control logic and required functions of the system?
Motor and PLC Integration and Interoperability
How easily can the new motor and PLC be integrated into the existing control system and industrial network?
Will the replacement PLC support the same or compatible communication protocols for seamless data exchange with other devices and systems?
PLC Programming and Configuration:
Is the programming software for the replacement PLC user-friendly and compatible with the existing programming environment?
How much effort and time will be required to migrate or rewrite the existing PLC programs for the new system?
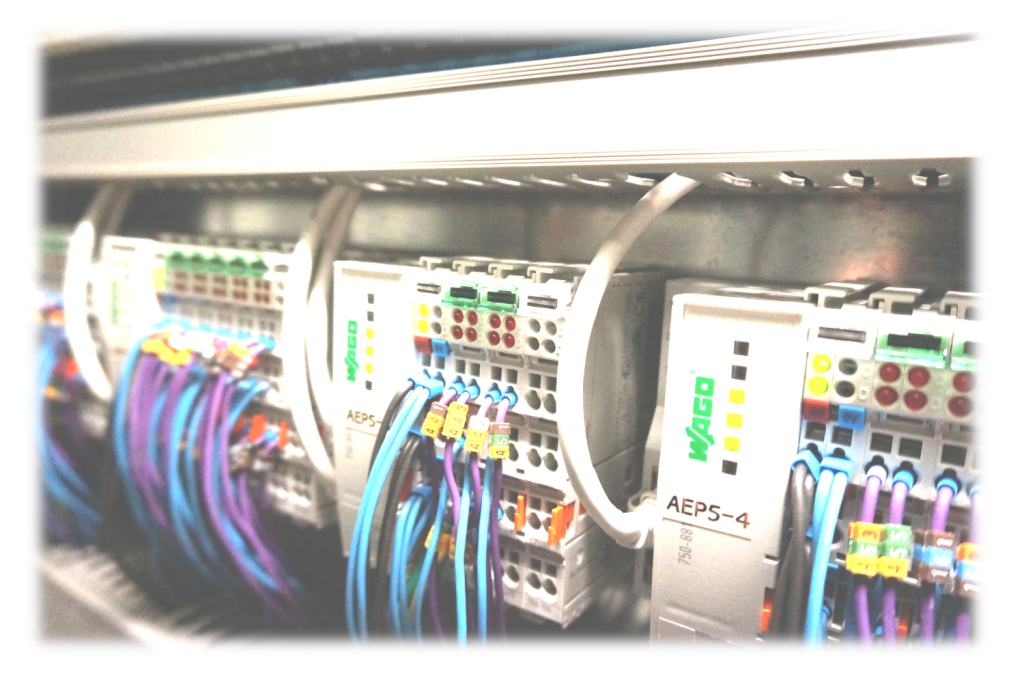
Electric Motor Energy Efficiency and Environmental Impact:
How does the energy efficiency rating of the new motor compare to the legacy motor, and what impact will it have on operational costs?
Are there any environmental considerations or regulations to be aware of when replacing the motor and PLC, such as energy efficiency standards or emissions requirements?
Cost and Return on Investment:
What are the upfront costs of purchasing and installing the new motor and PLC, and how do they compare to the potential savings in energy costs or improved productivity?
What’s the expected return on investment (ROI) and payback period for replacing the legacy equipment with more efficient and reliable alternatives?
Reliability and Maintenance:
What is the expected lifespan and reliability of the new motor and PLC, and how do they compare to the legacy equipment?
Are spare parts readily available for the replacement motor and PLC, and what’s the manufacturer’s support policy for maintenance and repairs?
Consider these questions when replacing legacy electrical motors and PLC controls. This will maximize the benefits of your new equipment.