You get a competitive edge by automating manufacturing, and PLC-based motor control systems can help. Programmable logic controls motor-driven equipment to complete tasks.
Looking For PLC Parts?
Get PLC QuoteSell To Us
Got Electrical Equipment You Don't Need?

Reduce Your Electrical Inventories & Earn Cash
Sell My EquipmentPanelboard
Need a Panelboard for Your Project/Job?

Our Experienced Sales Engineers Can Help Design the Right Panelboard For You
Learn MoreTransformer Oil Testing
Is Your Transformer Due For Servicing?

Get Your Oil Analysis & Fluid Testing Done By Our NETA-Certified Techs
Learn MoreElectrical Product Resources
Product Training Product Safety Product Guides Product News Featured Products- Introduction to Motor Control Using PLCs
- PLC Automation For Motors
- Solid State PLC Devices Transform Manufacturing
- Components of PLC-Based Motor Control Systems
- Benefits of Industrial Control Using Programmable Logic
- Technologies and Applications in PLC-Based Motor Control
- Future Trends in PLC-Based Motor Control
- Best Practices for Automating Motor Control
Introduction to Motor Control Using PLCs
A whole new era of motor control has emerged with the introduction of motor control using PLCs. They work as your specialized manufacturing computer, automating electromechanical processes by controlling machinery on factory assembly lines.
Using PLC motor control best practices, you can program these devices to execute specific tasks based on input from sensors and other devices, giving precise control over industrial processes. Previously, you might have dealt with controlling these motors using manual switches and relays, which led to inefficiencies and limited flexibility.
PLC Automation For Motors
Motor control systems were once operated by discrete parts and hardwired electronics. These technologies didn’t have the adaptability and scalability required in today’s advanced manufacturing environments. PLC-based motor control systems change the way we handle motors.
PLC-based motor control systems give you greater control capabilities by utilizing the power of digital technology. These systems control motor speed, direction, and other parameters by software programming rather than physical wiring or manual adjustments. This adaptability enables customizing motor control to your unique production needs, resulting in higher productivity and efficiency.
Motor control using PLCs offers smooth integration with actuators, sensors, and human-machine interfaces (HMIs), among other automation components. Because of this connectivity, you can monitor and get feedback in real-time, which helps detect problems early on and then take action before they get out of hand.
The flexible nature of PLC motor control is one of its main benefits. PLCs can be customized to fit many kinds of applications, like managing a conveyor belt in your warehouse or controlling the temperature in a chemical processing facility. They’re essential equipment for your daily industrial processes because of their adaptability.
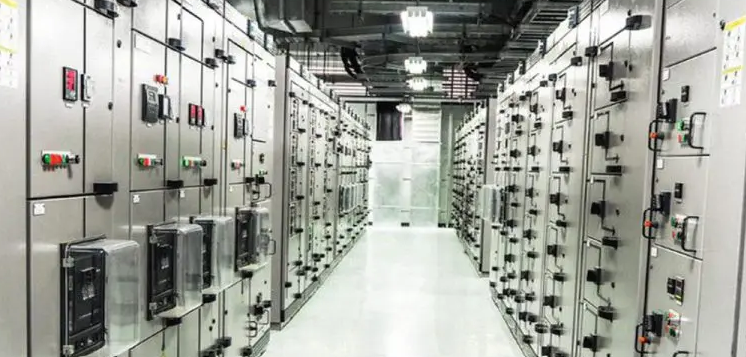
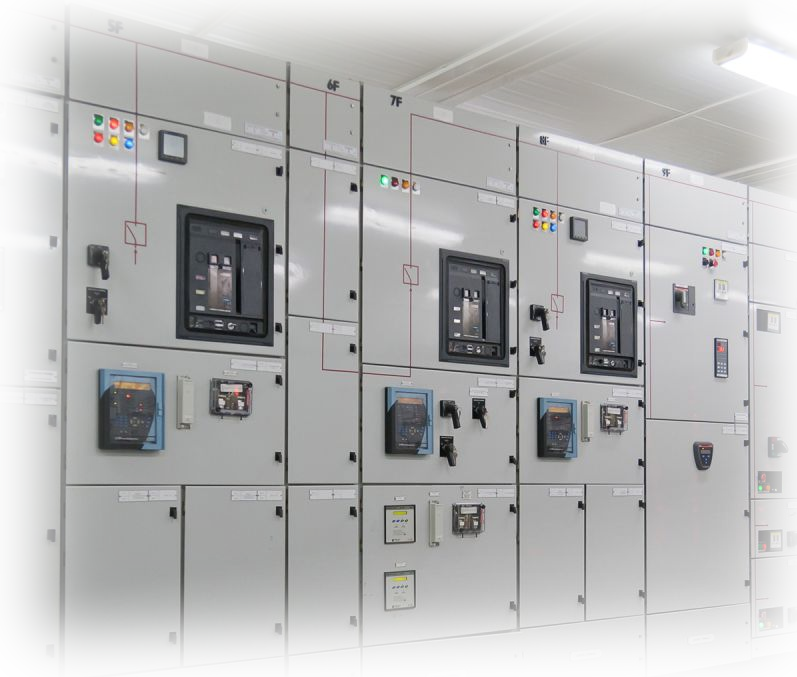
Solid State PLC Devices Transform Manufacturing
Following PLC motor control best practices provides several benefits for dependability and maintenance in addition to their versatility. Unlike conventional control systems, which have moving components and are subject to deterioration, PLCs are solid-state electronics. We can enjoy less downtime and spend less on maintenance, which improves your total operational efficiency.
All things considered, PLC-based motor control systems have completely transformed the manufacturing market by providing previously unheard-of degrees of accuracy, adaptability, and dependability.
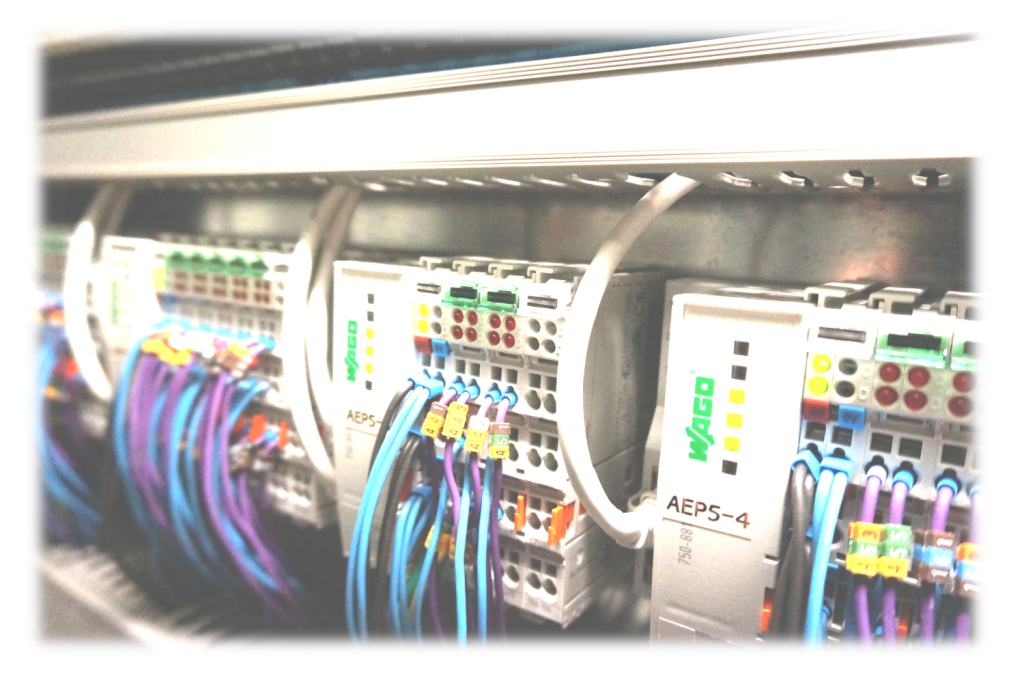
Components of PLC-Based Motor Control Systems
PLCs in motors depend on components that work together.
Benefits of Industrial Control Using Programmable Logic
PLC systems increase manufacturing efficiency.
Technologies and Applications in PLC-Based Motor Control
Technology | Description | Example Application |
Integration with IIoT | Real-time data interchange and remote monitoring are made possible by the Industrial Internet of Things (IIoT), which provides smooth connectivity between PLCs, sensors, and other devices. | Monitoring temperature and humidity levels in a manufacturing facility using IoT sensors connected to PLCs. |
AI and Machine Learning | AI algorithms are able to recognize patterns, maximize motor performance, and anticipate maintenance requirements by analyzing massive volumes of data produced by PLC-based automation for motors. | Predicting equipment failure based on motor performance data collected by PLCs and analyzed using AI algorithms. |
Predictive Maintenance | Industrial motor control with PLCs can reduce downtime and provide proactive maintenance plans by using machine learning algorithms and data analytics to predict equipment failures before they happen. | Implementing a predictive maintenance schedule for conveyor belts based on vibration data collected and analyzed by PLCs. |
Cybersecurity | Cybersecurity measures are crucial to safeguarding against potential cyber threats and maintaining the integrity of manufacturing operations as PLC-based systems grow more interconnected. | Implementing firewalls and encryption protocols to protect PLC-based systems from cyberattacks and unauthorized access. |
Future Trends in PLC-Based Motor Control
PLC-based motor control systems will keep integrating with cutting-edge technologies like machine learning, artificial intelligence, and the Internet of things. Better decision-making processes, predictive maintenance capabilities, and expanded data analytics will all be made possible by this combination.
Prioritizing Energy Efficiency and Sustainability: Industrial motor control with PLCs is giving attention to energy efficiency as environmental responsibility and sustainability become more important. Sophisticated optimization methods and control algorithms will help reduce energy use while increasing output.
Adoption of Cloud-Based PLC Solutions: As a way of remotely managing, programming, and monitoring motor control systems, cloud-based PLC solutions will become more common. Especially for scattered industrial operations, this remote access capabilities will allow better flexibility and scalability.
Extension of Applications in Diverse Industries: In addition to traditional manufacturing, PLC-based motor control systems will find use in the healthcare, agricultural, and renewable energy sectors. In a variety of operational scenarios, these solutions will allow for increased automation and efficiency.
Best Practices for Automating Motor Control
Extensive System Planning and Design: Give your manufacturing processes and requirements a careful evaluation before putting in place industrial motor control with PLCs to ensure optimal performance. Create a thorough system design that takes into consideration all required parts and features.
Installation and commissioning done correctly: Confirm that the motor control modules and PLC hardware are installed and configured correctly. Before deploying the system, make sure it is functioning properly by going through the testing and commissioning processes thoroughly.
Frequent Updating and Maintenance: To maintain optimal performance from your PLC-based motor control system, set up a proactive maintenance strategy. Update firmware and software frequently to fix security flaws and guarantee compatibility with new technologies.
Instruction for Maintenance Workers and Operators: To guarantee that operators and maintenance staff are competent in operating and troubleshooting the PLC-based motor control system, provide them thorough training. Give them the tools they need to quickly detect and fix problems, reducing downtime and interruptions.