Electric motor starters are critical components of motor control because they manage the power supply to motors. They support a smooth and regulated start while protecting the motor and linked systems. An electric motor starter functions as a motor’s ignition key, managing power flow to guarantee a safe and efficient start. This function is crucial in preventing sudden starts and protecting both the motor and the related gear from unnecessary stress.
Each electric motor starter is designed for a specific motor size and application. Understanding the alternatives enables you to select the right motor starter based on the intended usage, from the simple Direct-On-Line (DOL) starters ideal for smaller motors to the complex Soft Starters that support steady acceleration.
In this post, we’ll discuss essential maintenance practices for electric motor starters. This will help you identify defective starters through key indicators like prolonged cranking and unusual sounds during the startup process.
Need Motor Starters?
Get Starter QuoteSell To Us
Got Electrical Equipment You Don't Need?

Reduce Your Electrical Inventories & Earn Cash
Sell My EquipmentPanelboard
Need a Panelboard for Your Project/Job?

Our Experienced Sales Engineers Can Help Design the Right Panelboard For You
Learn MoreTransformer Oil Testing
Is Your Transformer Due For Servicing?

Get Your Oil Analysis & Fluid Testing Done By Our NETA-Certified Techs
Learn MoreElectrical Product Resources
Product Training Product Safety Product Guides Product News Featured ProductsSymptoms of a Bad Electric Motor Starter
A faulty electric motor starter can have negatively impact the overall operation of the motor system. It’s critical that you identify problems as soon as possible to avoid future consequences. Ignoring the signs of a defective motor starter might result in extended cranking, putting additional strain on the motor and even damaging related equipment.
The results of ignoring starter motor problems can lead to unexpected shutdowns, reduced efficiency, and even irreversible damage to the motor. Addressing these issues as soon as possible not only assures you get smoother motor functioning but also saves money on repairs and downtime.
Prolonged cranking, where the motor takes an unusually long time to start, often indicates a starter motor problem. Intermittent starting issues, characterized by inconsistent motor activation, are also common symptoms that should not be overlooked. Excess starter cranking can be caused by worn-out contacts or a malfunctioning solenoid in the starter. Intermittent starting problems can also reveal issues with the relay for the motor starter or damaged motor starter wiring. Recognizing these symptoms is your first step towards effective motor starter troubleshooting.
Understanding Noises During Electric Motor Startup
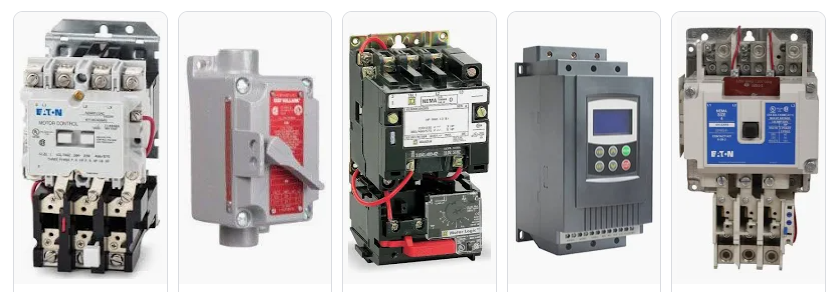
Grinding, clicking, or buzzing sounds may reveal more profound issues that must be addressed. Grinding noises indicate mechanical wear while clicking sounds suggest a problem with the solenoid. Buzzing sounds might indicate your motor starter has a faulty relay or damaged components. Interpreting these strange noises allows motor control technicians to identify the issue and perform repairs before it worsens.
A burning odor or smoke around the engine is an obvious sign of problems. Overheating within the starting motor can cause these dangerous signs, requiring immediate attention, and ignoring warnings risks additional motor damage and safety problems. Responding quickly to the problem improves the safety of both the motor system and your surrounding work environment.
Deciphering Overload Protection Trips in Electric Motor Systems
Overload protection is a necessary safety feature in motor systems. If your protective system trips frequently, this might be a red flag indicating a problem with the electric motor starter. Understanding the link between overloads and starting difficulties is essential for troubleshooting success.
Continuous overloading can cause overheating, increased component deterioration, and, in severe circumstances, motor failure. Recognizing the effects of repeated overload tripping allows you to take the right action, preventing additional damage to the motor system.
Inconsistent Electric Motor Speeds and Performance
Faulty electric motor starter issues can directly impact motor speed and performance dependability. Worn-out contacts, broken motor starter wiring, or malfunctioning solenoids can all disturb the motor’s smooth acceleration, resulting in speed inconsistency. Recognizing and addressing these issues will extend the life of your electric motor starter.
Motor speed or performance inconsistency might emerge as abrupt changes or erratic operation. Regular monitoring and fast detection of these signals allow personnel to make timely repairs, helping the motor system’s dependability.
Inspecting and Testing Electric Motor Starters
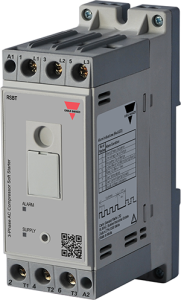
Visual examination is an integral part of identifying starter motor problems. Visually checking your starting motor step by step might reveal wear, corrosion, or loose connections. Also, an introduction to fundamental test methods gives technicians the skills they need to diagnose defects effectively.
Inspect components, including the solenoid, contacts, and wiring, while visually evaluating the starting motor. Basic diagnostic procedures, like continuity checks and voltage readings, give you significant information about the starter’s health. Combining visual examination and testing improves the faulty electric motor starter troubleshooting diagnosis process.
Troubleshooting Steps for Motor Starter Problems
A motor starter troubleshooting checklist is handy for identifying and addressing starter motor problems. It outlines common causes, such as worn-out electrical contacts, damaged wiring, or malfunctioning relays. Solutions and potential repairs for identified issues equip technicians with the knowledge to restore the starter motor to optimal performance.
The checklist guides technicians through a systematic troubleshooting approach, ensuring no potential issue goes unnoticed. A list streamlines diagnostic and corrective processes, from identifying the root cause to implementing the necessary repairs.
Faulty Electric Motor Starter Troubleshooting Checklist
1. Check power supply: Ensure the motor starter receives the proper voltage and there are no power interruptions or fluctuations.
2. Inspect circuit breakers and fuses: Examine the circuit breakers and fuses attached to the motor starter. Check for tripped breakers or blown fuses and replace them as needed.
3. Inspect wire connections: Inspect all wiring connections, particularly those between the motor starter and the motor, to ensure they are secure and free of damage or corrosion.
4. Check control signals: Inspect the control signals, such as start/stop buttons or control relays, to check they are working properly and providing the necessary signals to the motor starter.
5. Check overload protection: If the motor starter has built-in overload protection, ensure it is correctly configured without causing the motor to trip needlessly.
6. Examine the motor’s thermal protection: If the motor has its own thermal protection devices, such as thermal overloads or temperature sensors, ensure they work properly and do not cause the motor starter to trip.
7. Inspect motor windings: Look for evidence of damage or overheating, such as burned or discolored spots on the wires. Then, use a multimeter to check for continuity and insulation resistance.
8. Lubricate bearings: Lubricate the motor starter’s bearings if appropriate. Inadequate lubrication can increase friction and create motor starting problems.
9. Test auxiliary devices: If any auxiliary devices, such as interlocks or limit switches, are connected to the motor starter, ensure they work properly.
10. Consult the manufacturer: If the troubleshooting methods do not resolve the problem, contact the motor starter’s literature or the manufacturer for more direction or support.
Electric Motor Starter Preventive Maintenance Tips
The key to maintaining electric motor starters is preventive maintenance. Keeping the starter healthy and avoiding overloads are two specific recommendations for preventing starter motor difficulties. Routine maintenance increases the lifespan of the starting motor and reduces the chance of unexpected breakdowns. A proactive approach to maintenance is necessary for dependable motor systems.
Starter Type | Typical Applications |
Direct-On-Line (DOL) Starters | DOL starters are used in applications where the motor can handle full voltage at startup. Often in smaller motors for fans, pumps, and conveyor belts. |
Star-Delta Starters | Best for larger motors, these starters reduce inrush current during startup, minimizing mechanical stress. Found in industrial settings for heavy-duty machinery. |
Soft Starters | Used when a gradual motor acceleration is required, reducing mechanical and electrical stress. Usually seen in conveyor systems, pumps, and other sensitive applications. |
Variable Frequency Drives (VFDs) | Versatile starters are used for applications requiring variable speed control. Widely used in manufacturing, HVAC systems, and pump control for energy-efficient operations. |
Autotransformer Starters | Efficient for moderate-sized motors, they find applications in various industrial processes where controlled voltage reduction during startup is necessary. |
Wye-Delta Starters | Used in applications where a reduced voltage start is necessary to minimize inrush current and mechanical stress. Common in industries with large motors like water pumps. |
Electronic Motor Starters | Found in various applications where precise control and protection features are required, like complex machinery and equipment. |
Part-Winding Starters | Suitable for motors with two separate windings, these starters are found where reduced voltage starting is necessary to minimize stress on the motor. |
Reversing Starters | Employed in applications where the motor needs to operate in both directions. Typically in conveyor systems and machinery requiring bidirectional movement. |
Starter Panels with PLC Control | Systems incorporating PLC control are ideal for automation processes in complex industrial setups requiring sophisticated control and monitoring capabilities. |
—————–
We’ve covered essential maintenance of electric motor starters. This post should help you detect defective starters by recognizing indicators such as extended cranking and strange sounds during startup. Your toolset now includes a basic understanding of the impact of variable motor speeds and the need for visual examination and testing motors and starters. With this information, you can better analyze and solve starter-related motor issues in your electrical system. At Relectric, we supply motor starters and other electrical parts to help you with your projects. We’re here to help! 800.497.6255
IMPORTANT: Electrical systems can be hazardous, and working with them without the necessary expertise and training can be dangerous. If you’re not a qualified electrician or don’t have experience diagnosing a bad starter, it’s highly recommended to get the assistance of a certified electrical professional. Performing electrical work without the needed knowledge and training may lead to severe injuries, electric shocks, or damage to the equipment. Always prioritize safety and, when in doubt, contact a qualified electrician about how to replace a bad electrical starter and related electrical maintenance.