Are you looking to replace an electric motor starter? Think of electric motor starters as the coordinators of power and precision. They help produce a safe and efficient start. Magnetic Motor Starters and Manual Motor Starters control and protect electric motors and their connected electrical gear in what can be a harsh environment.
We’ve previously covered how to identify symptoms of a faulty motor starter. In this post, we’ll provide a step-by-step guide on how to replace electric motor starters that have failed. But before we look at repairing and replacing electric motors, let’s introduce two starter categories: Magnetic Motor Starters and Manual Motor Starters.
Need Magnetic or Manual Starters?
Get a QuoteSell To Us
Got Electrical Equipment You Don't Need?

Reduce Your Electrical Inventories & Earn Cash
Sell My EquipmentPanelboard
Need a Panelboard for Your Project/Job?

Our Experienced Sales Engineers Can Help Design the Right Panelboard For You
Learn MoreTransformer Oil Testing
Is Your Transformer Due For Servicing?

Get Your Oil Analysis & Fluid Testing Done By Our NETA-Certified Techs
Learn MoreElectrical Product Resources
Product Training Product Safety Product Guides Product News Featured ProductsMagnetic Motor Starter Basic Components and Features
Magnetic motor starters use electromagnetic forces to control the motor’s electrical circuit. The two main components of these starters are contactors and overload relays featured below.
Features of Magnetic Motor Starters
- Contactor-Based Operation: Magnetic starters use a contactor to control the flow of energy to the motor. The contactor’s magnetic coil energizes, shutting the contacts and starting the motor.
- Overload Protection: Magnetic starters with overload relays check the motor’s current. Magnetic starters with overload relays check the motor’s current.
- Remote Control: Magnetic starters usually have auxiliary contacts that support remote control and monitoring, making them good for applications where manual operation isn’t suitable.
- Automatic Reset: If a temporary overload occurs, magnetic starters with automatic reset features can restart the motor when the overload condition is complete, minimizing downtime.
- High-Power Applications: Magnetic motor starters are great for high-power applications because of their rugged design and ability to handle larger currents.
Manual Motor Starters Basic Components and Features
Manual motor starters call for human involvement to start or stop the motor. These starters are simpler in design and have applications in situations where manual control gets the job done.
Features of Manual Motor Starters
- User-Friendly Operation: Manual starters are straightforward, having a simple ON/OFF switch or a push-button for motor control.
- Cost-Effective: Manual motor starters can be less expensive than magnetic starters, making them an economical budget-conscious choice.
- Compact Design: With a simpler design, manual starters are typically compact, helping with installation with space constraints.
- For Small Motors: Manual starters are common in small motor applications where the simplicity of manual control meets the need, like in small machinery.
- Limited Overload Protection: Some manual starters have basic overload protection. Their main focus is on manual control. For greater overload protection, magnetic starters are usually better.
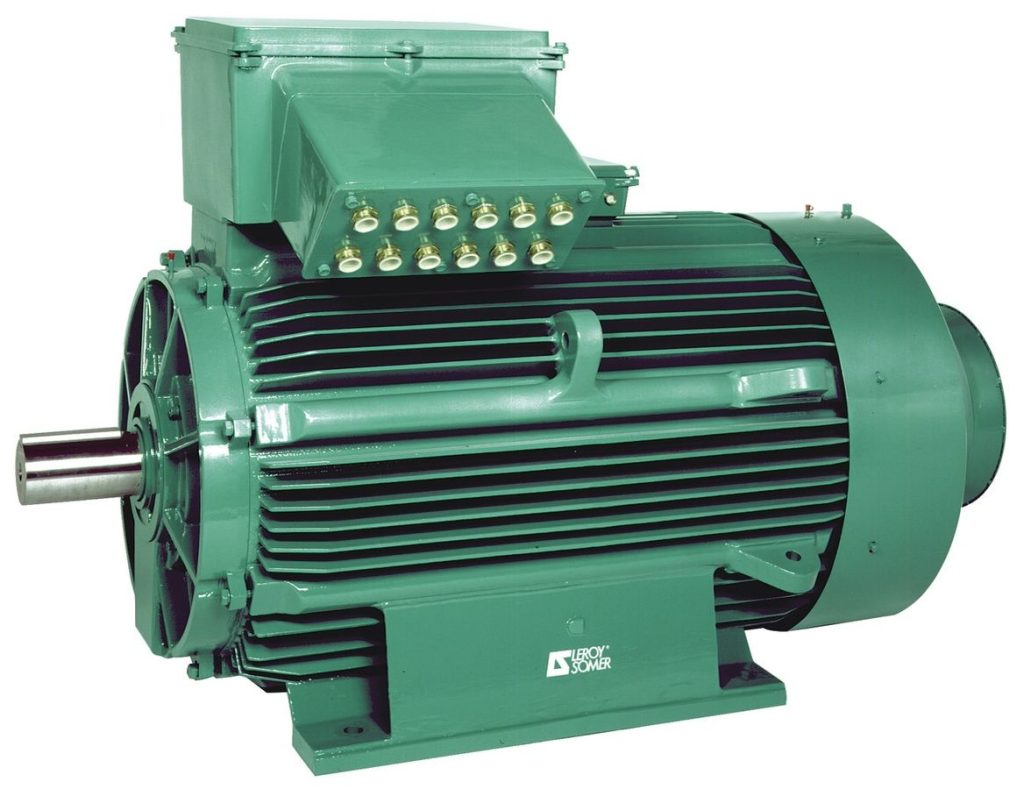
Steps to Replacing Electric Motor Starters
Safety First: Before replacing an electric motor starter, ensure the power is completely off. Lock out and tag out the electrical supply to the motor to avoid accidents.
Identify the Existing Starter: Note the specs of the existing starter, including voltage, current rating, and type. This information will help you choose the correct replacement starter.
Gather Tools: Get needed tools like screwdrivers, pliers, and wrenches. Also, have the replacement starter on hand.
Disconnect the Wiring: Carefully disconnect the wiring from the existing starter. Take pictures or label the wires to help you reconnect them correctly later.
Remove the Old Starter: Unbolt and remove the old starter from its mounting location. Be careful with any attached components or accessories.
Inspect and Clean: Check for signs of wear or damage on the mounting surface. Clean the area to ensure a secure connection for the new starter.
Mount the New Starter: Securely mount the new starter in the. Tighten the bolts evenly for proper alignment.
Connect Wiring: Connect the wires to the new starter based on your earlier notations or photos. Double-check connections to avoid mistakes.
Power On Test: With everything securely connected, turn the power back on. Verify the starter engages properly without any unusual sounds or issues.
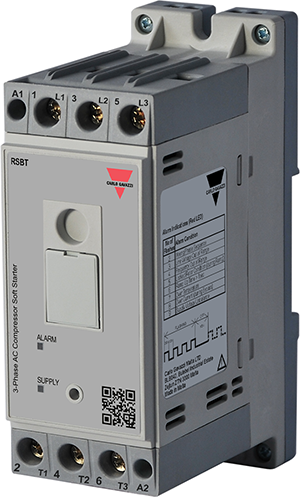
Adjust Settings: If your new starter has adjustable settings, make needed adjustments based on the motor manufacturer’s specifications.
Final Inspection: Perform a final inspection of your installation. Look for loose connections, exposed wires, or any abnormalities.
Document the Replacement: Update your equipment records with details of the replacement. Note the date, reason for replacement, and any related information for future reference.
Restore Normal Operations: Once you’re confident in the installation, remove any locks and tags and communicate with your staff that the motor is back online.
5 Starter Types, How They Work, Where They’re Used
Starter Type | How it Works | Used In |
Direct-On-Line (DOL) Starters | Directly connects the motor to the power supply, providing full voltage during startup. | AC induction motors for small to medium-sized applications, such as pumps, fans, and conveyor systems. |
Star-Delta Starters | Initially starts the motor in a low-voltage “star” configuration, then switches to full voltage to reduce starting current. | Larger AC induction motors in industrial settings, including heavy-duty pumps, compressors, and industrial fans. |
Autotransformer Starters | Uses an autotransformer to vary voltage during startup, reducing the inrush current. | Moderate-sized AC induction motors, applied in conveyor systems, mixers, and other equipment with moderate load demands. |
Soft Starters | Gradually increases voltage to the motor, minimizing mechanical and electrical stress during startup. | AC induction motors where a smooth start is needed, like conveyor belts, crushers, and large fans. |
Variable Frequency Drives (VFDs) | Controls motor speed by adjusting the frequency of the power supply, giving precise speed control and energy savings. | AC induction motors of various sizes and applications, including pumps, compressors, fans, and systems with variable load requirements. |
Electronic Motor Starters | Has solid-state components for precise motor control and protection, usually with advanced diagnostic features. | Diverse industrial applications with AC induction motors, including pumps, fans, conveyors, and equipment requiring advanced diagnostics. |
Starter Panels with Inverter Technology | Combines motor starters with inverter technology for energy-efficient control and variable speed operation. | AC induction motors where optimized performance and energy consumption are critical, such as HVAC systems, compressors, and manufacturing equipment. |
What You Should Know About Fixing Motor Starter Problems
So now we’ve reviewed the role of electric motor starters as coordinators of motor power and precision. Most importantly, you understand their place in supporting secure and efficient motor startup. Refer to the step-by-step guide next time you’re replacing a failed motor starter. Remember, it’s always good to consult with a qualified electrician or technician if at any point you’re unsure about a step on how to replace an electric Motor starter.
At Relectric, we supply motor starters and other electrical parts to help you with your projects. We’re here to help! 800.497.6255.
IMPORTANT: Electrical systems can be hazardous, and working with them without the necessary expertise and training can be dangerous. If you’re not a qualified electrician or don’t have experience diagnosing a bad starter, it’s highly recommended to get the assistance of a certified electrical professional. Performing electrical work without the needed knowledge and training may lead to severe injuries, electric shocks, or damage to the equipment. Always prioritize safety and, when in doubt, contact a qualified electrician about how to replace a bad electrical starter and related electrical maintenance.