Electric motors are used to power everything, and they rely on sophisticated control methods behind the scenes. Electrical relays and electrical contactors are two such key components in electric motor control. In this blog post, we’ll look at the distinctions between an electrical contactor versus electrical relay for motors and explain how to use contactors and relays in your electric motor control applications.
Need Contactors or Relays?
Get Your QuoteSell To Us
Got Electrical Equipment You Don't Need?

Reduce Your Electrical Inventories & Earn Cash
Sell My EquipmentPanelboard
Need a Panelboard for Your Project/Job?

Our Experienced Sales Engineers Can Help Design the Right Panelboard For You
Learn MoreTransformer Oil Testing
Is Your Transformer Due For Servicing?

Get Your Oil Analysis & Fluid Testing Done By Our NETA-Certified Techs
Learn MoreElectrical Product Resources
Product Training Product Safety Product Guides Product News Featured ProductsWhat’s an Electrical Relay, How Does it Work?
Electrical relays in motors play an important role in electric motor control circuits. They are small, adaptable devices that play an important role in controlling the flow of energy to a motor. Motor relays are essentially electromagnetic switches. When an electrical current is given to the relay’s coil, a magnetic field is created, which closes or opens the relay’s contacts. Motor relays can perform a variety of duties, including starting, stopping, and reversing electric motors, thanks to this simple yet effective technology.
Motor relays are frequently used for low-power, signal-level control applications. Motor relays, for example, can control the opening and closing of light-duty equipment such as lighting, fans, and pumps.
One of the main benefits of motor relays is their versatility in performing various control functions. Electromagnetic Relays (EMR) are the most common type of relays and use an electromagnet to switch contacts mechanically.
They come in various configurations, including SPST (Single Pole, Single Throw), SPDT (Single Pole, Double Throw), DPST (Double Pole, Single Throw), and DPDT (Double Pole, Double Throw).
“Throw” simply refers to the number of power sources involved. For example, “double throw” means two power sources are involved in the situation.
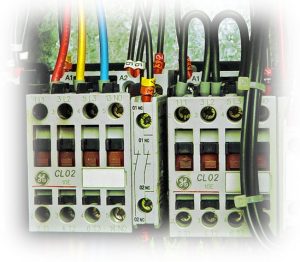
Understanding Electrical Contactors in Electric Motors
Electrical contactors are more sturdy devices designed to control high-power electric motors. They are motor control’s heavyweight champs. Contactors are made up of an electromagnetic coil that, when activated, pulls a series of contacts down to close the circuit.
Because contactors are designed to withstand the mechanical and electrical demands of heavy-duty applications, they are the ideal choice for managing electric motors in industrial and commercial environments. These devices are typically substantially larger in size than motor relays and can handle much higher currents and voltages.
Contactors are more built to resist the frequent use and high loads required by electric motors. Their capacity to handle high currents, which can range from tens to thousands of amperes, makes them ideal for motor control applications.
Key Differences Between Electrical Relays and Electrical Contactors
Understanding electrical contactors versus electrical relays is critical when deciding on the best device for your electric motor control requirements. Motor relays are built for low-power applications, while contactors can withstand high currents and voltages. Relays are small and compact, whereas contactors are larger and more robust.
Contactors are built to last and can withstand many on/off cycles over a lengthy period of time. Motor relays come in a variety of layouts for specific purposes, whereas contactors include several auxiliary contacts for advanced control capabilities.
Choosing Contactors and Motor Relays
Electrical contactors versus Electrical Relays: To put these differences into perspective, let’s explore some practical use cases for both motor relays and contactors:
Motor Relays: These devices are ideal for low-power applications like home automation, automotive control systems, and signal-level control. For example, in a smart home, motor relays can control the operation of window blinds or garage door openers.
Contactors: Contactors shine in high-power electric motor control scenarios. They are commonly found in industrial equipment, such as conveyors, pumps, and large HVAC systems. In commercial buildings, contactors are used to control elevator motors, large air conditioning units, and manufacturing machinery.
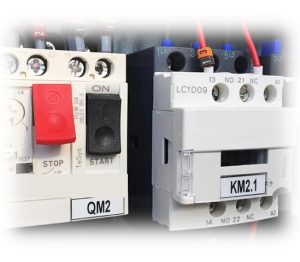
Factors to Consider When Sizing Contactors and Motor Relays
Several factors need to be explored when deciding whether to use motor relays or contactors in your electric motor control application:
Load Requirements: Consider your electric motor’s power requirements. Motor relays work well for low-power applications, whereas contactors are required for high-power applications.
Control Logic: Determine the control functions that your system will require. Contactors can give more extensive control functions than relays for simple on/off control.
Environmental Conditions: Consider the environment in which the devices will be used. Contactors with a more durable structure may be more suited for rugged conditions or outdoor use.
Cost and Maintenance: Consider the original cost as well as the long-term maintenance requirements. Although relays are frequently more cost-effective, contactors may be a better investment in high-use cases.
Sizing an Electrical Relay for an Electric Motor
Factor to Consider | Relay Type (e.g., Electromagnetic Relay, Solid-State Relay) |
Current Rating | [Your Relay Type & Current Rating] |
Voltage Rating | [Your Relay Type & Voltage Rating] |
Load Type | [Your Relay Type & Recommended Load Type] |
Switching Frequency | [Your Relay Type & Recommended Switching Frequency] |
Durability and Lifespan | [Your Relay Type & Durability Characteristics] |
Size and Mounting Options | [Your Relay Type & Size/ Mounting Options] |
Environmental Conditions | [Your Relay Type & Recommended Environments] |
Additional Features | [Your Relay Type & Notable Features] |
Cost | [Your Relay Type & Estimated Cost] |
Ease of Maintenance | [Your Relay Type & Maintenance Considerations] |
Typical Applications | [Your Relay Type & Common Heavy-Duty Motor Applications] |
Sizing an Electrical Contactor for an Electric Motor
Factor to Consider | Contactor Type (e.g., AC Contactor, DC Contactor) |
Current Rating | [Your Contactor Type & Current Rating] |
Voltage Rating | [Your Contactor Type & Voltage Rating] |
Pole Configuration | [Your Contactor Type & Number of Poles] |
Horsepower (HP) Rating | [Your Contactor Type & HP Rating] |
Coil Voltage | [Your Contactor Type & Coil Voltage] |
Enclosure Type | [Your Contactor Type & Recommended Enclosure] |
Duty Cycle | [Your Contactor Type & Recommended Duty Cycle] |
Size and Mounting Options | [Your Contactor Type & Size/ Mounting Options] |
Environmental Conditions | [Your Contactor Type & Recommended Environments] |
Overload Protection Options | [Your Contactor Type & Overload Protection Features] |
Additional Features | [Your Contactor Type & Notable Features] |
Cost | [Your Contactor Type & Estimated Cost] |
Ease of Maintenance | [Your Contactor Type & Maintenance Considerations] |
Typical Applications | [Your Contactor Type & Common Heavy-Duty Motor Applications] |
Electrical Contactors for High Power, Relays for Low Power
We’ve dug into the realm of motor relays and contactors in this discussion, examining the key differences, applications, and aspects to consider when selecting the correct device for your electric motor control needs.
Motor relays, the electrical world’s nimble and versatile switches, are the go-to solution for low-power applications and signal-level control. They can be found in home automation, automotive systems, and other applications where precision is critical.
Contactors, on the other hand, are the heart of electric motor control and are built to handle high-current, heavy-duty applications. They shine in industrial machinery, commercial buildings, and other applications that require the physical force of electric motor control.
Consider the load needs, control logic, and environmental circumstances specific to your application as you make your decision. Contactors give unrivaled reliability and longevity, while relays provide flexibility and cost-effectiveness.
Finally, deciding between motor relays and contactors comes down to matching the correct tool to your individual demands. You can ensure the effective and reliable operation of your electric motor control systems by studying the subtleties of each device and evaluating your requirements.